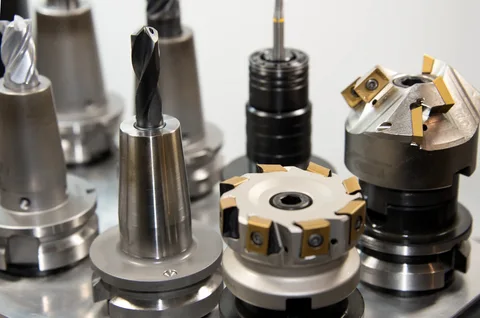
5 Common Mistakes to Avoid When Using CNC Cutting Tools
CNC (Computer Numerical Control) cutting tools have revolutionized the manufacturing process, allowing for precise and efficient machining of materials like metal, wood, and plastics. However, while CNC technology has transformed industries, improper usage of CNC cutting tools can lead to significant issues such as tool wear, machine malfunction, and compromised product quality. It is essential for operators and manufacturers to understand the common mistakes that can occur when using these tools. By identifying and avoiding these errors, businesses can save time, money, and resources while achieving the best possible results.
This article explores five common mistakes that individuals make when using CNC cutting tools, along with tips on how to prevent them. Understanding these pitfalls will help improve performance, extend the life of machinery and tools, and ensure the highest standard of precision in every project. Whether you are a seasoned operator or a beginner, these insights will guide you toward more effective and efficient machining practices.
Using Incorrect Speeds and Feeds
The first mistake many CNC operators make is setting the wrong speeds and feeds for the cutting tools. The term “speeds and feeds” refers to the cutting speed (how fast the tool moves) and the feed rate (how fast the material moves into the cutting tool). These settings depend on a variety of factors, including the material being cut, the type of CNC cutting tools used, and the depth of the cut. Incorrect speeds and feeds can cause excessive tool wear, reduced cutting efficiency, and poor surface finishes on the workpiece.
To avoid this mistake, always consult the manufacturer’s recommendations for the specific CNC cutting tools being used. Experimenting with different settings can be useful, but it is important to understand the limits of the tool and the material being machined. Additionally, using a calculator or software designed to help with speed and feed calculations can ensure that these variables are optimized for each job, reducing the chances of wear and tear and ensuring better results.
2. Failing to Properly Calibrate the CNC Machine
Another common mistake when using CNC cutting tools is failing to properly calibrate the CNC machine. Calibration ensures that the machine is aligned correctly, with all components working in harmony. If the CNC machine is not calibrated, it can lead to poor accuracy, misaligned cuts, and inconsistent results. Inaccurate tool paths or improper positioning of the cutting tool can compromise the entire machining process, leading to material waste, costly rework, and reduced efficiency.
To prevent this issue, it is crucial to regularly check and calibrate the CNC machine before starting any job. This includes verifying that the machine’s axes are square, the tool is properly positioned, and the workpiece is secure. Many modern CNC machines have built-in calibration functions that make this process easier, but it’s still essential to understand the fundamentals of machine calibration and to perform it regularly to maintain accuracy and quality.
3. Ignoring Tool Wear and Tear
Tool wear is an inevitable part of CNC machining, but many operators overlook the signs of tool degradation until it’s too late. Over time, CNC cutting tools can become dull, chipped, or damaged, which can lead to poor cutting performance, heat generation, and even tool breakage. If left unchecked, worn tools can result in defective parts, higher scrap rates, and unnecessary downtime. It’s important to monitor the condition of the tools and replace them before they reach a critical point of wear.
To avoid this mistake, establish a regular tool inspection schedule. This includes checking for signs of wear such as blunt edges, discoloration, or any physical damage to the tool. It’s also essential to track how many hours the tool has been in use, as most tools have a recommended lifespan based on usage. Investing in a tool wear monitoring system or using CNC machines equipped with tool wear detection features can help alert operators to potential issues before they become major problems.
4. Improper Tool Selection
Using the wrong CNC cutting tools for the job can lead to suboptimal performance and undesirable results. Different cutting materials, thicknesses, and processes require specific types of tools, each designed with particular geometries and coatings to optimize cutting efficiency. For instance, using a general-purpose drill bit for a high-speed cutting operation can lead to poor surface finishes, excessive wear, and even tool breakage. Additionally, selecting the wrong tool can also lead to higher levels of vibration, reducing precision and increasing the likelihood of damage to both the workpiece and the machine.
To avoid this mistake, always select the appropriate CNC cutting tools based on the material, geometry, and machining process you are working with. Consult the tool manufacturer’s specifications and the machine’s capabilities to ensure compatibility. It is also beneficial to invest in a variety of specialized tools that can handle different types of materials and cutting tasks, ensuring better results and minimizing downtime.
5. Inadequate Coolant Usage
The role of coolant in CNC machining cannot be overstated. Coolant helps reduce friction between the cutting tool and the workpiece, preventing overheating, tool wear, and distortion of the material. However, many operators fail to use the correct amount of coolant or neglect its importance altogether. Insufficient coolant can lead to excessive heat buildup, which not only shortens the life of CNC cutting tools but also affects the quality of the finished product. On the other hand, using too much coolant can cause splashing, affect surface finishes, and create a mess.
To avoid this mistake, ensure that the coolant system is working properly and that the correct type and amount of coolant are used for each machining operation. Make sure the coolant is clean and free from contaminants, as dirty coolant can damage both the tools and the workpiece. Additionally, monitor the coolant flow rate and pressure to ensure that it is sufficient for the specific cutting operation. Using a high-quality coolant that is compatible with the material being cut will help improve cutting efficiency, prevent overheating, and extend the life of both the tools and the machine.
Conclusion
CNC cutting tools are essential to achieving precise and high-quality machining results, but improper usage can lead to costly mistakes. By avoiding the common errors outlined above—incorrect speeds and feeds, improper calibration, ignoring tool wear, poor tool selection, and inadequate coolant usage—you can maximize the efficiency and lifespan of your CNC equipment. Regular inspection, proper maintenance, and selecting the right tools for the job will ensure that your CNC operations run smoothly and produce superior results every time.
By understanding the fundamentals of CNC cutting tools and following best practices, operators can minimize the risk of errors, reduce downtime, and maintain high levels of precision in their work. Whether you are just starting or are an experienced professional, avoiding these mistakes will contribute to more successful machining processes, enhanced product quality, and a more efficient production cycle.